Additives for paints and varnishes – problem solver for a successfull switch to waterbased coatings
Dr. Nicholas Büthe, MÜNZING CHEMIE GMBHSalzstr. 174, D-74076 Heilbronn, Germany
1 Introduction
Paints, varnishes, adhesives and other similar coatings are systems which contain numerous different components. During the preparation of these systems the components do not undergo chemical reactions but they can have (at least physical) effects on each other. In the easiest case the final product posess properties which are a sum formed out of the properties of the single ingredients. But most often the different components have an influence on each other. Especially in the formulation of environment-friendly water based coating these effects may occur as such formulations are normally more complex than solvent based ones. Additives which are specially designed for water based coatings offer a toolbox to eliminate these effects which may arise in the switch from solvent to water based systems. Using the right additive, problems in production and application of a paint can be solved as e.g. foam formation, bad application behaviour or insufficient pigment stabilization.
2 Defoamer
Foam is a (stable) dispersion of gas in a liquid system and surfactants are necessary in order to stabilise a gas bubble in an aqueous environment.
Problems caused by foam are:
- Production vessels are not optimally filled,
- Dispersing process is inefficient,
- Formation of pinholes,
- Reduced protection,
- Reduction of gloss and transparency,
- Negative effect on levelling,
- Optical aspect negative.Therefore an additive is necessary in order to destroy the foam or to prevent foam formation. Defoamers are such products which act in a physical way and not in a chemical way and which are incompatible with the system to defoam (Fig. 1).
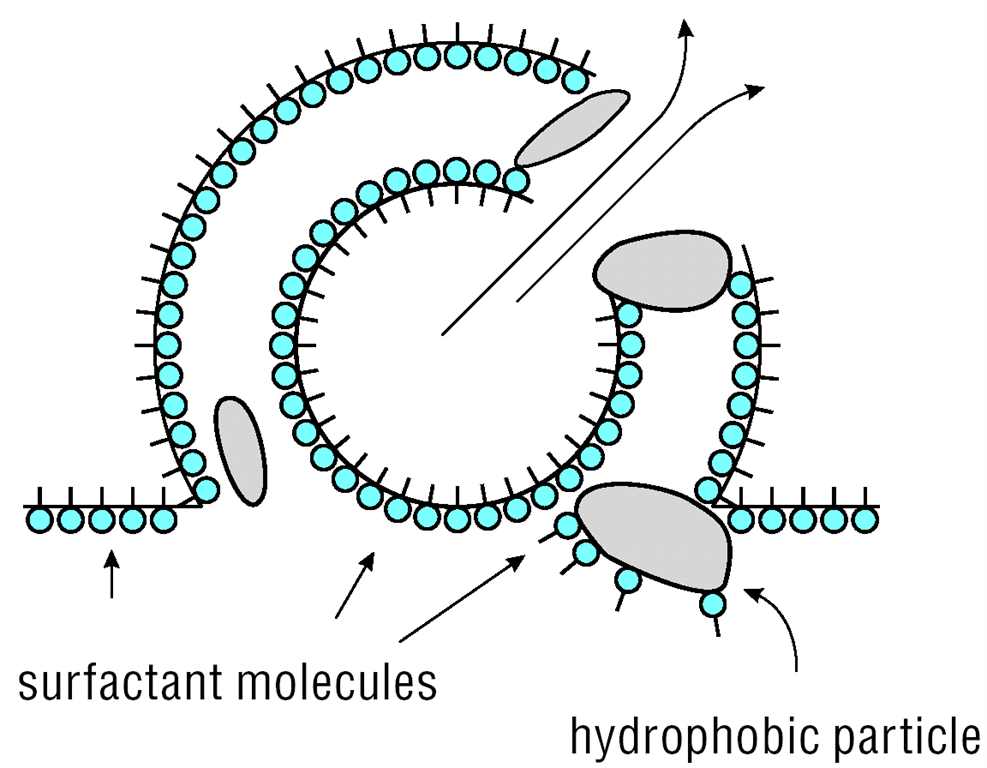
Fig. 1. Action of a defoamer
However: the right balance has to be found between compatibility and efficiency. As the selection of the defoamer is influenced by the components of the formulation and as the defoamer has an influence on the formulation itself it is nearly impossible to predict and select the right product without empirical tests. AGITAN® defoamer tables for different applications, the online selection guide on the MÜNZING CHEMIE homepage based on binders or technical service in the lab - as all provided by MÜNZING CHEMIE – are the efficient tools to find the right product.
3 Rheology modification
Rheology is the behaviour of a substance under the external pressure/force to escape from this external pressure. An additive to modify these properties of a paint is called thickener colloquially but should be better called rheology modifier as it modifies and controls its production and application behaviour. Rheological Modifiers influence a lot of properties as e.g. sagging, leveling, gloss, colour strength, hiding power, spatter (Fig. 2), brush drag, sedimentation and pigment stabilization.
Fig. 2. Spatter resistance of a emulsion paint
A rheology modifier has to be selected and adjusted in dosage for the application. Therefore the full rheology profiles of paints at different shear rates and dosages of modifier have to be measured and compared as offered by the technical customer service of MÜNZING CHEMIE. Determinations of viscosity at fixed shear rates, like with Ford cup or Brookfield viscosimeter, are not enough to understand the rheolgical behaviour of a paint e.g. during storage or in the application process.
4 Pigment dispersion and stabilization
The dispersing process consists of three steps:
- Wetting of pigment surfaces - Displacement of absorbed air from particle surface
- Destroying of agglomerates - Acting of mechanical forcesStabilisation of dispersion - Prevention of reagglomerationDispersants are the additives which enable, promote and boost these steps giving storage stable paints with full color strength. They stabilize the pigment during and after the dispering process using a sterical and/or electrostatical mechanism (Fig. 3).
Fig. 3. Sterical and electrostatical pigment stabilization
Unsufficient pigment stabilization would cause aggregates or agglomerates remain in the paint, rub-out effect, low colour strength, poor flow or loss of gloss.
Again it is not ease to predict the suitable dispersant for a specific pigment and the amount of dispersant needed for sufficient stabilization. Normally time consuming lab tests have to be carried out. These are offered as a service from MÜNZING CHEMIE as well as an online database on the homepage which can be searched with pigment name, supplier name or color index number. Also pigment paste guide formulation are available without a registration procedure.
5 Summary
The right additive added in the right amount is very often the efficient solution to problems in the production, storage or application of a paint. Mostly very small amounts are enough to improve properties significantly or to make it possible to produce a paint at all with the given production equipment.
Especially in the switch from solvent to water based paints and varnishes severall new problems arise which did not exist before. Foam formation is much stronger and sufficient pigment stabilization in general is harder to achieve. But with the online tools of the MÜNZING web page (
www.munzing.com ) and the technical service staff for customer problems this successful switch is possible and pays off. MÜNZING additives are creating the additive value!